8 Tons Per Hour Asphalt Plant Gas Steam Boiler Technical Specifications and Quotation
2022-04-06 08:51:32
Specifications and Quotation
Design, supply, construction, installation, commission, start-up And training of two identical boilers at Benghazi asphalt plant.
Introduction
This offer presents the technical specifications and the quotation of : design, supply, install, training, commissioning and start-up of two identical complete fire tube steam boilers with (associated equipment). Natural gas / F.O firing burners, the boiler shall be design to achieve reliable and highly efficient operational performance being strongly and simply.
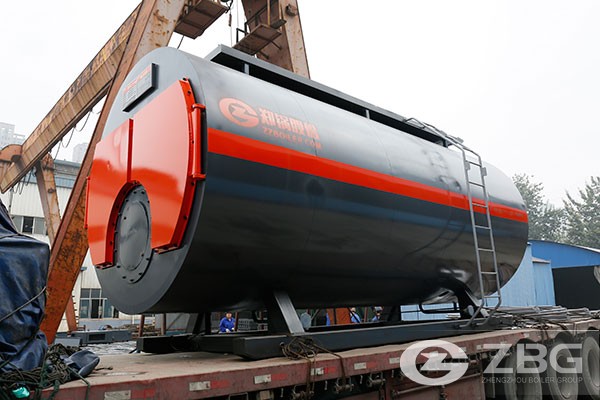
wns oil & gas fire tube boiler
System components:
- Scotch type steam boiler
- Burner
- Steam exit valve
- Bottom blowdown drain valve
- Bottom blowdown shut off valve
- Manual surface blowdown valve
- Boiler feed water pump group
- Boiler water inlet valve
- Boiler water inlet check valve
- Safety valve
- Boiler automatic water level control system
- Reflex glass boiler water indicator
- Pressure switch
- Pressure transmitter
- Manometer and manometer valve
- Boiler temperature sensor
- Exhaust gas temperature sensor
- Vacuum breaker and shut off valve
- Electrical control board
- Packaging and preparation for shipment
- Start up and commissioning
- Water softener
- Feed water storage (condensate) tank
- Chimney (optional)
- Automatic bottom blowdown system
- Automatic surface blowdown system
- Sample cooler
- Boiler feed water heating economizer
- Thermic deaerator system
- Steam header (optional)
- Advantages
- Large steam storage of scotch type boilers allow continuous and adequate steam supply and user does not encounter any problems during sudden steam drafts.
- Exhaust gas temperature is decreased and efficiency is increased by the 3 pass design
- Heat Transfer Surface is provided exactly and accurately.
- Unit thermic load is kept in proper limits by the help of accurately calculated and applied heat transfer surface. This way boiler life time is prolonged, explosion risk is decreased and efficiency is increased.
- In reverse flame design fire/smoke leaves the boiler at once while in 3 pass systems it travels in boiler along three passes. By this way useful heat in boiler tubes is transferred to water fully. Also as the heat transfer area is less in reverse flame boilers, the steam production capacity is limited. Three pass design eliminates such disadvantages and provides relatively long boiler life time.
- Steam production capacity: Max. 8000 kg/h (F&A 100 o C)
- Heat Transfer Area: 200 m2 Total
- Thermal Capacity: 5.000.000 kcal/h ~5814 KW
- Boiler Efficiency: over %90 at full load (W/O Economizer)
- Fuel Type: Natural Gas
- Lowest Heating Value of Fuel Natural Gas: 8250 kcal/Nm3
- Max. Fuel Consumption: 673, 4 Nm3/h (at cold start)
- Max. Needed Installed Power: 38 kW
- Operating Pressure: 16 bar
- Design Pressure: 18, 4 bar
- Hydrostatic Test Pressure: 31, 74 bar
- Saturated Steam Temperature: 204 °C
- Applied Standards: 2014/68 EU - EN12953 - EN13445-3
- Certificates: CE
- Metal Plate Quality: P265GH - P295GH - P355GH (HI - HII) quality, EN10204 3.1 or EN10204 3. Certificated boiler steel plates and proper carbon steel plates are used according to design and standards' directives.
Fire Tube Quality EN10216 Seamless Boiler Tubes
Welding Quality Welds during manufacturing are carried out by welders certificated according to EN9606.
Welding Tests Welds are tested according to rates and methods directed in EN 12953 and EN5817 Level B standards as Ultrasonic, Magnetic Particle, Radiographic, Penetrant and Visual. ULTRASONIC Test are applied by Level 2 certificated staff according to EN 9712. Our Level 2 certificates are given by TOA NDI / Japan and TÜV / Germany
Isolation 80 kg/m3 dense, 100 mm thick, rabitz wired, rockwool covered with PVC coated, min. 0,7 mm thick galvanized steel
Approximate Boiler Dimensions (W/O accessories and empty)
- Length 7100 mm
- Width 3100 mm
- Height 3300 mm
- Weight 18700 kg